mercredi 28 octobre 2020
Interview avec EMI WISSLER
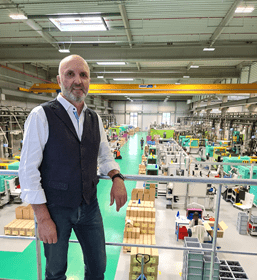
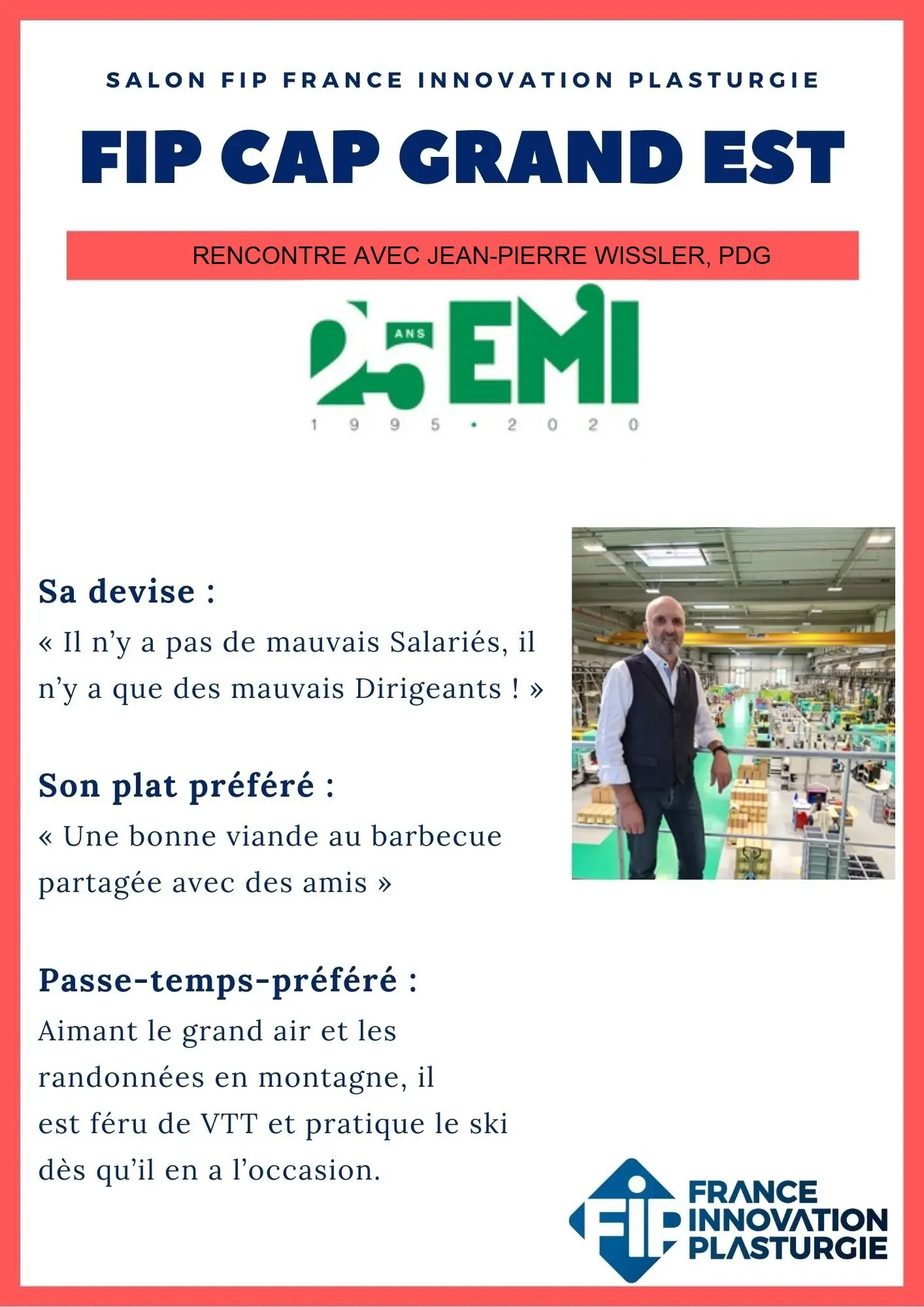
Quelles sont les forces de votre entreprise ?
« Être un partenaire pour nos clients »
Grâce à notre concept d’accompagnement global, le 360° Full Plastic Concept, nous offrons un véritable soutien à nos clients. Chaque projet débute par l’étude et le développement des produits, viennent ensuite la conception et la fabrication des outillages, puis l’injection et le surmoulage des pièces et pour finir, nous gérons également l’assemblage et la validation d’ensembles et sous-ensembles. Par la suite, le laboratoire de mesures et d’essais réalise des contrôles complets afin de garantir une qualité absolue de toutes les pièces et ensembles avant livraison.
De plus, pour assurer un processus global, nous proposons des activités complémentaires de personnalisation comme le marquage, la magnétisation de ferrites, le contrôle caméra en ligne, les conditionnements spécifiques etc…
Quelles actions mettez-vous en place pour le développement durable ?
La certification 14001 témoigne de notre engagement à diminuer notre empreinte environnementale :
– Construction d’un bâtiment conforme aux règlementations en vigueur (réduction des émissions sonores, stockage internalisé, borne de charge pour véhicules électriques, proximité des transports en commun…)
– Consommation d’énergies électriques maitrisée grâce à des équipements écoresponsables
– Tri et valorisation des déchets
– Risque incendie maitrisé grâce à un bâtiment totalement sprinklé et des murs coupe-feux
– Construction d’un bâtiment conforme aux règlementations en vigueur (réduction des émissions sonores, stockage internalisé, borne de charge pour véhicules électriques, proximité des transports en commun…)
– Consommation d’énergies électriques maitrisée grâce à des équipements écoresponsables
– Tri et valorisation des déchets
– Risque incendie maitrisé grâce à un bâtiment totalement sprinklé et des murs coupe-feux
Quel regard portez-vous sur l’évolution de votre métier ?
Tout au long de mes 35 ans d’expérience dans le secteur de la plasturgie j’ai pu observer une évolution constante des méthodes de fabrication afin de rester dans une démarche d’amélioration et d’innovation en continu pour satisfaire les exigences client.
D’un métier de « pousse matière » nous sommes passés à des partenariats client/fournisseur afin de développer les solutions les plus adaptées aux produits.
Ceci a été possible notamment grâce à l’évolution des machines, de l’informatique (CAO, Rhéologie, ERP, suivi TRS) et à une intégration du développement en interne chez les plasturgistes.
Cette évolution du métier se poursuit et c’est au travers d’une maitrise de l’outil de production et de la capacité d’innover que les acteurs de la plasturgie continueront à évoluer.
Où sont situés vos marchés ?
Notre stratégie est de concentrer nos clients à proximité, en France, en Suisse et en Europe.
Quelles sont vos innovations marquantes ?
Nous sommes précurseurs dans l’injection hybride et le surmoulage de matériaux thermoplastiques chargés fibres de verre. Nous fabriquons des pièces en série en composites également appelés Organosheet. Ces matériaux permettent un gain de poids considérable tout en augmentant les performances mécaniques : résistance, fonctionnalisation etc….
Nous proposons également des solutions innovantes dans l’injection bi-matière avec la maîtrise des 4 principales technologies : core back, plateau rotatif, base rotative et transfert.
Quelles sont les évolutions organisationnelles dans votre entreprise ?
Tout au long de l’année 2017, des groupes « projet » internes ont été sollicités afin de créer ensemble, notre usine du futur dans laquelle nous avons emménagé en 2018.
Ainsi, tout a été pensé afin de faciliter l’organisation et le travail de chacun notamment pour l’optimisation des flux d’entrée et de sortie :
– Chariots de manutention autonomes (AGV)
– Centrale matière automatisée
– Système de surveillance de production par logiciel Cyclades
Ainsi, tout a été pensé afin de faciliter l’organisation et le travail de chacun notamment pour l’optimisation des flux d’entrée et de sortie :
– Chariots de manutention autonomes (AGV)
– Centrale matière automatisée
– Système de surveillance de production par logiciel Cyclades
Un objectif essentiel est également la mise en place d’une solution PLM (Product Lifecycle Management). Ce processus est actuellement en cours et permettra de développer et de gérer un produit en version 4.0.
Afin de continuer notre développement dans les secteurs médicaux et paramédicaux, nous accentuerons, dans les mois à venir, notre degré de certification avec la norme ISO 13485. Celle-ci permettra de répondre de manière encore plus complète aux exigences des dispositifs médicaux en constante évolution.
Marchés : Médical, Electrique, Connectique, Energies renouvelables, Bâtiment, Industrie, Automobile etc…
Savoir-faire : Spécialiste dans la transformation des matières thermoplastiques, composites et l’assemblage d’ensembles et de sous-ensembles pour ses clients.
Certifications : ISO 9001, ISO 14001 et UL, zone grise avec salle blanche ISO 8, ISO 13485 en cours
Employés : 180, trilingues FR-DE-EN dans certains services
Implantation :
Usine 4.0 de 17 000 m² depuis 2018
1 avenue Euroeastpark
68300 – Saint-Louis Neuweg
Tél : +33 (0)3 89 70 36 70 Mail : contact@emi-wissler.com
Usine 4.0 de 17 000 m² depuis 2018
1 avenue Euroeastpark
68300 – Saint-Louis Neuweg
Tél : +33 (0)3 89 70 36 70 Mail : contact@emi-wissler.com